Recycling wind turbine blades into high-value materials for carbon fiber production
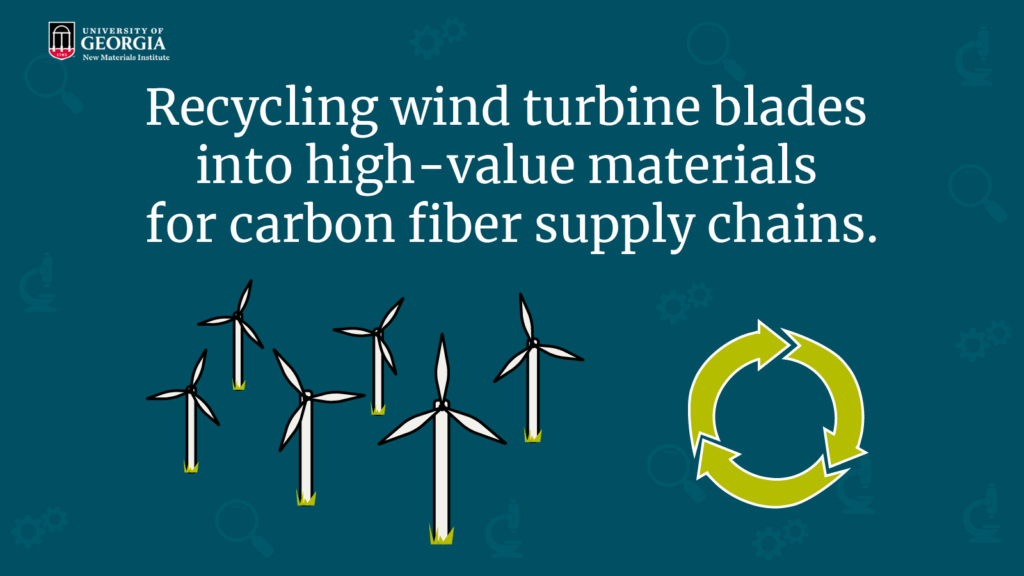
Is it environmentally sustainable to recycle decommissioned wind turbine blades to produce polyacrylonitrile, or PAN, fibers which are utilized in more than 90% of global carbon fiber production? Are there better routes to producing PAN fibers? A recent manuscript from a team at the UGA New Materials Institute utilized life cycle analysis, or LCA, to examine the sustainability of a novel coaxial layered fiber spinning process they created to recycle wind turbine blades.
Wind turbine technology expanded globally from 25 gigawatts to 651 gigawatts between 2001 and 2019, and associated waste is projected to grow from 789,000 tons in 2021 to 43 million tons by 2050, the authors said. Waste from decommissioned wind turbine blades is expected to reach 200,000 tons annually, with most of that going to landfills. Incineration of decommissioned wind turbine blades is an alternative option for disposal, but carries risks associated with air pollution and emissions of toxic pollutants.
In their LCA, the team compared greenhouse gas emissions across various scales of production in different regions of the world, including the United States and Europe. They found that regions with cleaner energy grids, such as those based on nuclear energy, could see greater reductions in their carbon footprint through their novel process for creating PAN fibers. PAN fibers are so versatile that they can be modified at the molecular level to fine tune properties that meet specific manufacturing requirements for the aerospace, automotive, and sports equipment industries.
Utilizing their novel coaxial layered fiber spinning process, the team generated about 100 g per production run at the laboratory scale, 100 kg for a mid-scale production run, and 1000 kg for a full-scale production run, and found that the larger the production scale, the smaller environmental impact the process has.
In assessing environmental impacts, their LCA, which followed International Organization for Standardization (ISO) guidelines (ISO 14040-14044), accounted for the entire PAN fiber creation production, the amount of energy required for each step of the fiber creation process, as well as ozone depletion, global warming, smog, acidification, eutrophication, carcinogenics, noncarcinogenics, respiratory effects and ecotoxicity.
Other possible avenues for lowering the environmental impact of wind turbine blade recycling include finding suitable green polymers with high carbon yields for raw materials and enhancing the efficiency of the carbonization and graphitization stages, which are the stages that require the largest amounts of energy.
The team’s manuscript illustrates the potential for upcycling decommissioned wind turbine blades into high-value precursors fibers for carbon fiber production; provides a basis for evaluating trade-offs in processing routes in fiber production; and emphasizes the broader implications of integrating recycled materials into carbon fiber supply chains.
“Life Cycle Analysis of Coaxial Layered Fiber Spinning for Wind Turbine Blade Recycling” was recently published in ACS Sustainable Resource Management and was coauthored by M. Taylor Sobczak, Gengyang Li, Arunachalam Ramanathan, Sri Vaishnavi Thummalapalli, Varunkumar Thippanna, Lindsay B. Chambers, Taylor Theobald, Hongyue Sun, Ke Li and Kenan Song, all from the UGA College of Engineering, and Stephen Nolet of TPI Composites. Ke Li is an associate professor whose research focuses on materials flow and life cycle assessment and Song is an associate professor whose research focuses on polymer science, composite engineering and 3d printing; both are faculty members in the UGA New Materials Institute.